Spis treści
- Prefabrykaty w budownictwie wielorodzinnym
- Jak projektować domy z prefabrykatów?
- Programy wspierające projektowanie z prefabrykatów
- Prefabrykaty - współpraca projektant - wykonawca - monter
- Stopień prefabrykacji w budynkach wielorodzinnych
- Prefabrykaty żelbetowe
- Elementy ścienne z prefabrykatów
- Stropy z prefabrykatów
- Prefabrykaty keramzytobetonowe
- Prefabrykaty drewniane
- Prefabrykaty i budownictwo modułowe
Prefabrykaty w budownictwie wielorodzinnym
Niestety w Polsce wciąż pokutuje przekonanie, że prefabrykaty przeznaczone do budownictwa wielorodzinnego, a tym samym wzniesione z nich domy, są nieatrakcyjne i kiepskie jakościowo. Współczesne technologie wytwarzania elementów prefabrykowanych (o konstrukcji betonowej, drewnianej lub stalowej) oraz ich montażu pozwalają wznosić budynki o bardzo dobrych parametrach technicznych i walorach architektonicznych. Użycie elementów prefabrykowanych znacznie przyspiesza wznoszenie budynku w porównaniu do technologii tradycyjnej. Precyzyjnie wykonane prefabrykaty powstają według szczegółowego projektu w fabryce, są dostarczane gotowe na budowę i dosyć łatwe w montażu. W dużym stopniu eliminuje to prawdopodobieństwo popełnienia błędu podczas wznoszenia obiektu.
Zależnie od możliwości wytwórcy można w nich wcześniej wykonać odpowiednią izolację i je wykończyć, a także wyposażyć, np. w otwory na instalacje, a nawet już w fabryce zamontować okna i drzwi. W przypadku ścian trójwarstwowych prefabrykowanych nie ma potrzeby prowadzenia dodatkowych prac ociepleniowych i wykończeniowych. Ogranicza to prace mokre do koniecznych robót montażowych, eliminuje przerwy technologiczne, a tym samym obniża koszty realizacji. Niektórzy producenci prefabrykatów proponują kompletne zestawy elementów wytwarzane według odpowiednio przygotowanego projektu dla konkretnej inwestycji. Zapewnia to nie tylko szybką realizację obiektu przy zachowaniu odpowiednich bardzo dobrych parametrów – izolacyjności termicznej i akustycznej, odporności ogniowej oraz trwałości. Pozwala również na dotrzymanie terminów i zazwyczaj zakończenie inwestycji zgodnie z planem.
Jak projektować domy z prefabrykatów?
Chociaż prefabrykaty mogą mieć niemal dowolne wymiary i kształty, najkorzystniejsze ekonomicznie jest zastosowanie standardowych rozwiązań przy jednoczesnej niskiej różnorodności elementów. Trzeba również wziąć pod uwagę takie aspekty, jak dostępność dróg dojazdowych i ich szerokość (skrajnię), a także rodzaj transportu oraz ciężar i gabaryty poszczególnych prefabrykatów. Te ostatnie parametry mają istotne znaczenie, ponieważ np. przy transporcie drogowym warunkowane są przepisami drogowymi. Wpływają zatem w istotny sposób na projektowanie wielkości elementów, gdyż prefabrykaty mieszczące się w limitach można przewozić bez konieczności uzyskiwania specjalnych zezwoleń.
Nie mniej istotna jest odległość od wytwórni prefabrykatów do miejsca ich wbudowania, która ma wpływ nie tylko na koszty transportu, lecz także stopień jego skomplikowania. Im bliżej jest zlokalizowany zakład produkcyjny i większa dostępność surowców, tym mniejsze nakłady związane z dostarczeniem elementów na plac budowy. Podczas projektowania budynku z prefabrykatów trzeba również pamiętać o odpowiednich maszynach, które będą potrzebne do ich montażu. Na przykład nośność dźwigu dobiera się, uwzględniając lokalizację budowy, możliwości zastosowania danego typu żurawia (wieżowego lub samochodowego) oraz dostępnego miejsca na budowie.
Prefabrykaty wykorzystywane do obiektów wielorodzinnych to często elementy wielkogabarytowe, dlatego projektant prefabrykatów musi starannie przeanalizować sposób pracy takiego elementu podczas jego transportu do miejsca docelowego wbudowania, przy uwzględnieniu oparcia na podporach tymczasowych.
Powinien on zatem – najlepiej już na etapie projektu – dobrać i usytuować systemowe akcesoria do podnoszenia i podparcia elementu, tak aby zastosowana technologia była bezpieczna dla ludzi znajdujących się w strefie montażu i samego prefabrykatu. Jest to bardzo istotne zwłaszcza w przypadku elementów, w których wykonano wycięcia o znacznych wymiarach lub ukosowanie w strefie podparcia.
Programy wspierające projektowanie z prefabrykatów
Obecnie dostępne nowoczesne technologie informatyczne w programach typu BIM znacznie przyspieszają proces projektowania i poprawiają jakość dokumentacji. Stworzony dzięki nim zaawansowany model 3D budynków pozwala bardzo precyzyjnie zaprojektować konstrukcję i jej prefabrykowane elementy.
Bezpośrednio z przygotowanego modelu otrzymuje się odpowiednie rysunki wykonawcze, montażowe, detale oraz zestawienia materiałowe. Programy te umożliwiają szybsze projektowanie i poprawiają jakość dokumentacji. Podczas montażu na placu budowy nie da się już wprowadzić poprawek, dlatego wszystko musi do siebie pasować.
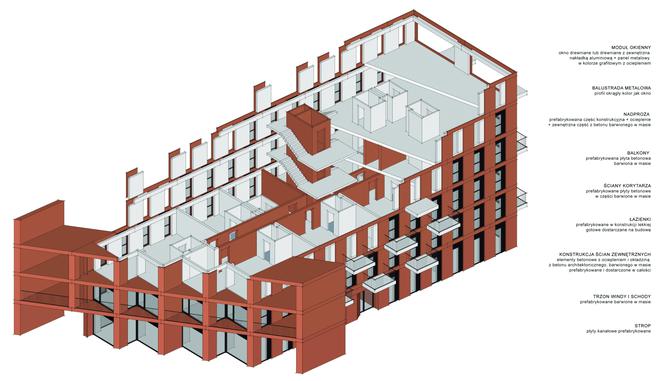
i
Prefabrykaty - współpraca projektant - wykonawca - monter
Przygotowanie optymalnego projektu budynków, w których wykorzystuje się prefabrykację, wymaga dobrej współpracy projektantów z różnych branż oraz wytwórcy prefabrykatów. Zagwarantuje to dopasowanie elementów konstrukcyjnych i zharmonizowanie ich dostaw na plac budowy.Jest to szczególnie istotne w przypadku wykorzystania do budowy elementów o wysokim stopniu prefabrykacji, wyposażonych w okna i drzwi, instalacje elektryczne, sanitarne i grzewcze.
Specjaliści muszą ustalić jeszcze w fazie projektu wiele szczegółów związanych z wymaganymi wymiarami poszczególnych otworów na stolarkę, trasami kablowymi, rodzajami puszek elektrycznych, a także przygotować konstrukcję pod systemy wentylacyjne, grzewcze bądź instalacje wodno-kanalizacyjne. Ta współpraca nierzadko zabiera sporo czasu, dlatego zaprojektowanie budynku w technologii prefabrykacji zwykle trwa dłużej niż w tradycyjnej. Czas wytworzenia prefabrykatów zależy głównie od stopnia skomplikowania elementów oraz możliwości technicznych i produkcyjnych wytwórni.
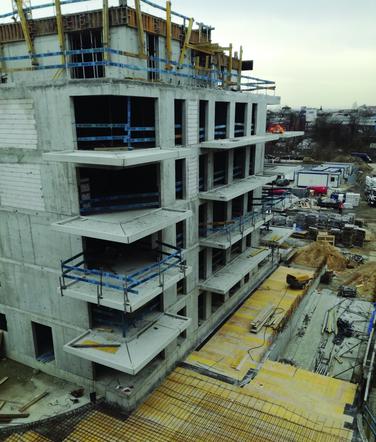
i
Stopień prefabrykacji w budynkach wielorodzinnych
W budynkach wielorodzinnych od dawna stosuje się elementy prefabrykowane, które znacznie przyspieszają proces budowy. W przypadku konstrukcji betonowych i żelbetowych zwykle są to belki sprężone, słupy, płyty stropowe (kanałowe, pełne, typu filigran), biegi schodowe i płyty balkonowe, które łączy się z elementami wykonywanymi w technologii monolitycznej lub tradycyjnej. Ich producenci często oferują również ściany 1-, 2- i 3-warstwowe z izolacją termiczną, wytwarzane według projektu w zakładzie produkcyjnym.
Nowoczesne ściany prefabrykowane standardowo mają zintegrowane wszystkie niezbędne kanały i przejścia pod instalacje, dzięki czemu na budowie nie trzeba wykonywać bruzd, a powierzchnia ściany jest nienaruszona i odpowiednio gładka. Mogą mieć również zamontowane fabrycznie drzwi, okna i parapety zewnętrzne. Duża dokładność montażu w warunkach zakładu produkcyjnego oraz odpowiednie ukształtowanie stref wokół okien pozwala wyeliminować mostki termiczne. Tak przygotowane elementy, poza spoinowaniem, po montażu praktycznie nie wymagają dodatkowych zabiegów. Można je od razu malować wewnątrz oraz prowadzić inne prace wykończeniowe.
Możliwe jest także staranne wykonanie całych fragmentów budynku, np. kabin sanitarnych czy szachtów windowych. Niektórzy wytwórcy proponują rozwiązania systemowe (nazywane czasami modułowymi), które pozwalają wykonać niemal wszystkie elementy budynku według precyzyjnie przygotowanego projektu. Wówczas trzeba je jedynie odpowiednio przetransportować i połączyć na budowie.
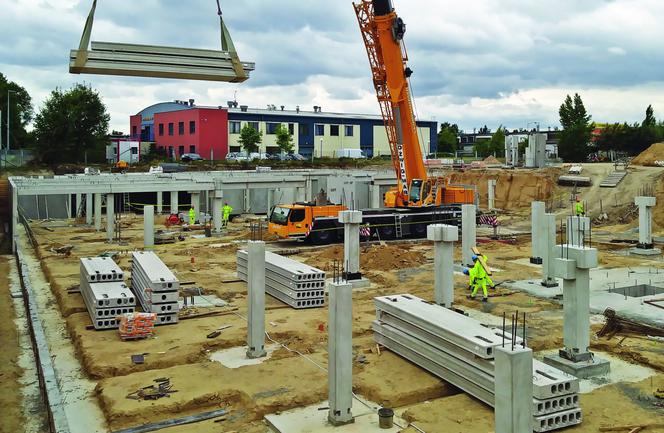
i
Prefabrykacja możliwa jest również w drewnianym budownictwie mieszkaniowym. Tu zwykle transportuje się np. gotowe, ocieplone lub przygotowane do wykończenia ściany oraz wiązary dachowe. Wysoki stopień prefabrykacji budynku oferuje technologia budownictwa modułowego.
W tym przypadku powstają całe fragmenty – moduły – budynku, np. kolejne segmenty mieszkań. Mogą być przygotowane w wykończenia wnętrz, wyposażone w sprzęty sanitarne, stolarkę okienną i drzwiową, a nawet wykończone niemal pod klucz. Zazwyczaj tego typu obiekty bazują na konstrukcji drewnianej lub stalowej, ocieplonej i wykończonej według życzenia klienta na podstawie precyzyjnego projektu.
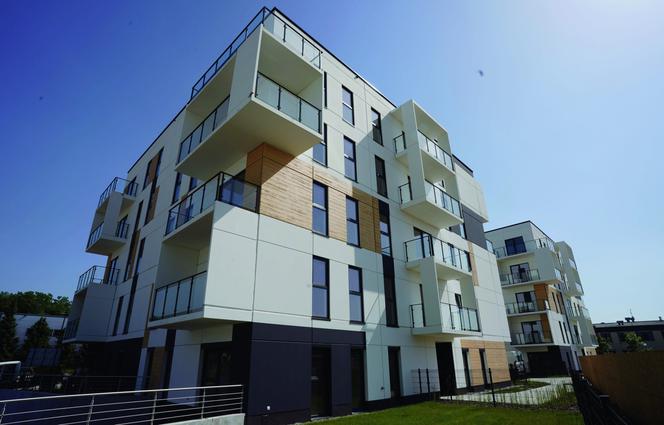
i
Prefabrykaty żelbetowe
Obecnie produkcja prefabrykatów jest sterowana przez komputery i systemy automatyki, co pozwala wytwarzać bardzo szeroki asortyment elementów konstrukcyjnych: poza podstawowymi elementami, jak belki, stropy czy biegi schodowe, a także ściany – od nośnych, z których można budować wielokondygnacyjne wieżowce, po cienkie na zaledwie dwa centymetry płyty elewacyjne. Coraz częściej stosowane są również balkony prefabrykowane, które mogą być od razu wykonane wraz z antypoślizgową powierzchnią górną ułożoną z zachowaniem spadku zapewniającego odwodnienie oraz z elementami umożliwiającymi odprowadzenie wody czy montaż poręczy.
Prefabrykacja pozwala ponadto na wykonanie balkonów o urozmaiconych kształtach, dużych wysięgach, a także narożnych. Możliwe są też realizacje płyt balkonowych w technologii szalunków traconych, gdzie prefabrykat płyty balkonowej, stanowiący równą i gładką powierzchnię dolną balkonu, zespolony jest z betonem uzupełniającym, układanym na miejscu budowy. Dostępne są również rozwiązania przyspieszające wykonanie łazienek, szachtów itp. w postaci prefabrykowanych przestrzennych elementów. Na przykład tzw. kabiny sanitarne wyposażane są na etapie prefabrykacji w komplet kanałów i przewodów instalacyjnych.
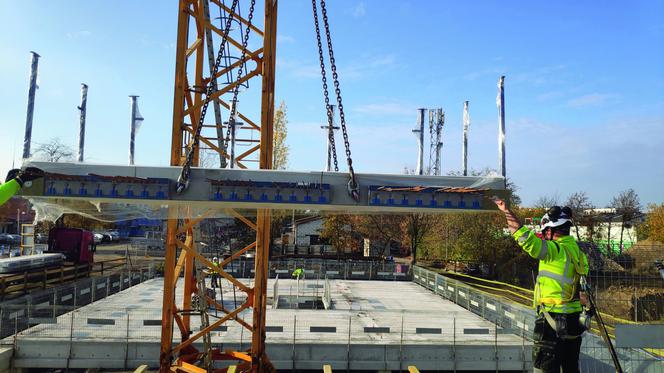
i
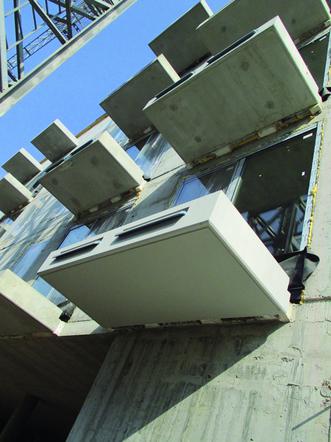
i
Elementy ścienne z prefabrykatów
Typy ścian wykorzystywanych w danej inwestycji i ich gabaryty projektowane są z uwzględnieniem wymagań klienta, możliwości logistycznych czy nośności dźwigu. W zależności od technologii wykonania i zastosowania są to elementy: jednowarstwowe (międzylokalowe, między drogami komunikacyjnymi i lokalami, klatek schodowych, szybu windowego, zewnętrzne – do dalszego wykończenia na budowie), dwuwarstwowe (zewnętrzne, między drogami komunikacyjnymi i lokalami), trójwarstwowe typu sandwich (zewnętrzne, między komunikacją i lokalami). W ścianach trójwarstwowych można zastosować dowolną izolację termiczną, dopasowaną do wymagań i specyfiki danego projektu, np. wełnę mineralną, styropian, piankę PIR lub neopor.
Elementy elewacyjne mogą mieć dowolną barwę, kształt i fakturę, np. kamienia, łupków, terakoty, marmuru lub według indywidualnego projektu. Zwykle ściany te mają następujące wymiary: długość: 6–8 m; wysokość: 2,8–3 m; grubość warstwy nośnej: 17–25 cm dla ścian wewnętrznych, 12–18 cm dla zewnętrznych; grubość warstwy elewacyjnej ściany trójwarstwowej: 4–7 cm. Ze względu na bardzo szerokie możliwości produkcyjne dostawców prefabrykatów w zasadzie nie ma ograniczeń co do wymiarów czy typów stosowanych ścian. Ograniczenia wynikają głównie z możliwości transportowych i montażowych w warunkach danej budowy.
Łączenie elementów ściennych z prefabrykatów
Poszczególne prefabrykaty ścienne mogą być łączone za pomocą strzemion, marek stalowych, pętli kotwiących typu VS lub zamków dyblowych. Można także wykonać połączenia spawane (choć są one już coraz rzadziej stosowane) lub wykorzystać złącza śrubowe – wbetonowane szyny i przykręcane do nich elementy łączące. Nowoczesnym i dość popularnym rozwiązaniem są zamki (kasety) lub szyny z pętlami linowymi, gotowe do wbudowania w prefabrykat podczas produkcji. Pozwalają na całkowite ukrycie połączenia w szerokości elementu oraz przeniesienie obciążeń we wszystkich trzech kierunkach. Te z pętlami odginanymi (sprężynującymi) umożliwiają montaż bez dodatkowego odginania ręcznego, a także umieszczenie prefabrykatu w luce między innymi segmentami. Tego typu złącza uzupełnia się odpowiedniej klasy betonem lub fabrycznie przygotowanymi mieszankami. Dzięki temu są one mniej narażone na korozję i bardzo trwałe.
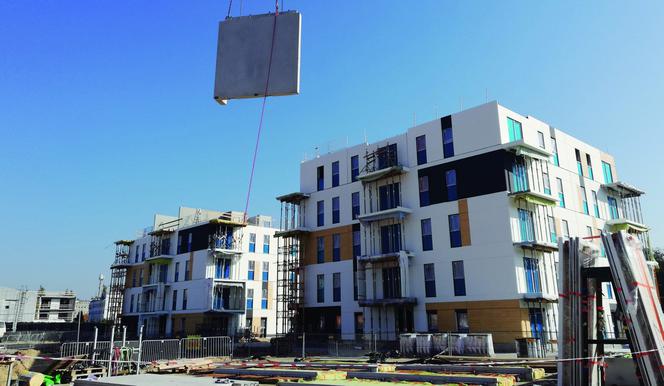
i
Kasety z pętlami powinny być umieszczane w formie tak, by pętle były ułożone jedna nad drugą w jednej linii (tolerancja wbudowania 20 mm), co wymaga dużej dokładności podczas produkcji prefabrykatu. Rozwiązanie to umożliwia wykonanie szczelnych i wytrzymałych złączy doczołowych, narożnych, typu T oraz połączeń ściany i słupa. Systemy kaset powinny być precyzyjnie zamontowane w formie do produkcji prefabrykatu. Dostępne są też systemy zapewniające równoczesne, szybkie i skuteczne połączenie elementów prefabrykowanych oraz łączników wbudowanych instalacji przez zwykłe zatrzaśnięcie. Wystarczy prosty montaż prefabrykatów na styk. Dodatkowo umożliwia to demontaż segmentów bez ich uszkodzenia.
Innym rozwiązaniem jest szalunek ciśnieniowy – system gotowych, stabilnych szyn stalowych z odpowiednio rozstawionymi pętlami linowymi, co eliminuje konieczność dopasowywania zamków. Szyny sąsiednich, łączonych ze sobą ścian mogą mieć (w zależności od systemu) taką samą lub różną głębokość. Rozwiązanie to zmniejsza zużycie zaprawy oraz umożliwia montaż w najcieńszych ścianach. Systemy kaset lub szyn są dobierane zależnie od rodzaju obciążeń, jakie będzie przenosiło połączenie prefabrykatów. Po ustawieniu ścian przez „oczka” pętli przeprowadza się odpowiednio dobrany pręt stalowy lub wygięte siatki zbrojeniowe. Najistotniejszym momentem montażu jest dokładne wypełnienie spoiny odpowiednio zagęszczoną zaprawą: zalewową – o bardzo wysokiej płynności i wytrzymałości, rozprowadzaną bez użycia pompy, oraz plastyczną – przeznaczoną do systemu szyn i długich zamków, wprowadzaną w spoinę za pomocą pompy.
Stropy z prefabrykatów
W budownictwie mieszkaniowym, niezależnie od konstrukcji ścian, powszechnie stosuje się stropy prefabrykowane, dające gładką powierzchnię sufitową, niewymagającą wyrównywania tynkiem. Najczęściej są to płyty stropowe pełne zbrojone i sprężane, stropy zespolone typu filigran i sprężane płyty kanałowe, np. typu HC. Te ostatnie cieszą się największą popularnością ze względu na niską cenę i łatwość montażu, a także wysoką efektywność projektowania i metod produkcyjnych, gładki spód oraz możliwość wyboru wysokości i nośności elementu. Wymagają niewielkiego zakresu konstrukcyjnych robót monolitycznych (złącza dyblowe i wieńce).
Trzeba jednak pamiętać, że stropy z tego typu płyt mogą przekrywać jedynie konstrukcje o kształcie prostokątnym. Większe możliwości dają płyty stropowe pełne lub typu filigran, wytwarzane niemal w dowolnym kształcie i wymiarach (nawet o rozpiętości do 12 m). Co istotne, można w nich także wykonywać otwory. Ważne jest, by dobrać odpowiednie zbrojenie i grubość stropu do jego rozpiętości i wielkości obciążeń. W procesie produkcji elementu możliwe jest np. umieszczenie dodatkowego zbrojenia na przebicie (w strefie przysłupowej, dla punktowego podparcia stropu) za pomocą specjalnych rusztów. Stropy typu filigran, przy znacznie większej pracochłonności na budowie (podparcie montażowe, duży zakres zbrojenia i robót monolitycznych), są częściej stosowane ze względu na możliwość wykonywania w nich wszelkiego rodzaju instalacji.
Połączenia elementów stropowych
Połączenia między prefabrykowanymi płytami stropowymi to zazwyczaj zamki dyblowe wypełniane betonem oraz zbrojone wieńce. Strop z płyt typu filigran wymaga dodatkowego zbrojenia, a także wykonania warstwy nadbetonu. Możliwe jest łączenie różnych rodzajów stropów w jednym budynku, np. płyt strunobetonowych oraz typu filigran, które po ułożeniu nadbetonu powinny mieć tę samą wysokość. Pozwala to na wykonanie stropów o skomplikowanym kształcie oraz prosty montaż balkonów. Płyty łączy się poprzez zbrojenie górne i nadbeton oraz tzw. połączenie młotkowe (wpusty wycięte w panelu).
W stropach prefabrykowanych w miejscach zespolenia z płytą balkonową stosuje się łączniki balkonowe (koszyki izolacyjne) z warstwą izolacji cieplnej i odpowiednio przygotowanym zbrojeniem. W stropach typu filigran można fabrycznie wykonać otwory. W przypadku płyt pełnych lub kanałowych sprężonych trzeba stosować wymian stalowy, który przenosi obciążenie z podpieranej płyty (maksymalnie do rozpiętości 10 m) na sąsiednie. Dostępne są również jego wersje specjalne przeznaczone do płyt kanałowych z wnękami do poprowadzenia instalacji (np. w łazienkach) oraz miejsc, w których płyty są różnej wysokości. Na rynku dostępne są stropy prefabrykowane wykonywane ściśle według konkretnego projektu, łączone bezspoinowo systemem zamknięć, który napina płyty stropowe oraz tworzy trwałą i sztywną konstrukcję, przenosząc siły tnące z płyty na płytę. W tego typu stropach przestrzenie do wykonania kanałów kablowych są fabrycznie przygotowane, można w nich również zamontować rury elektroinstalacyjne i puszki (np. do oświetlenia). System pozwala na realizację stropu o dowolnym kształcie, otworach i wydrążeniach, można z nim połączyć różne konstrukcje schodów, a także zamocować warstwę izolacji akustycznej.
Możliwe jest również zamontowanie samonośnego balkonu montażowego zintegrowanego z konstrukcją stropu, który pozwala na szybkie połączenie płyty balkonowej z łącznikiem zapobiegającym tworzeniu się mostków termicznych pomiędzy balkonem a stropem. Wśród dostępnych na rynku stropów prefabrykowanych wyróżniają się płytowe, ze zintegrowanym systemem ogrzewania bezkonwekcyjnego, które równomiernie ogrzewają lub chłodzą, nie powodując wirowania cząsteczek pyłu. Do klimatyzacji pomieszczeń wykorzystują zasadę wymiany promieniowania cieplnego, umożliwiającą całopowierzchniowe wyrównywanie temperatury w bardzo krótkim czasie. W tym systemie cała dolna powierzchnia masywnego stropu służy do efektywnego i wydajnego ogrzewania i chłodzenia. Pozwala to – w porównaniu ze zwykłym ogrzewaniem konwekcyjnym – zaoszczędzić ok. 30% energii i kosztów. Dostępna jest także wersja stropu przygotowanego fabrycznie do montażu typowych systemów wentylacyjnych w ukrytych kanałach (zintegrowany system rur do montażu instalacji napowietrzającej i odpowietrzającej) z wylotami przygotowanymi podczas produkcji elementów stropowych.
Prefabrykaty keramzytobetonowe
Domy jednorodzinne z prefabrykatów keramzytobetonowych są już znane od wielu lat, również w Polsce, chociaż na naszym rynku nie cieszą się jeszcze dużą popularnością. Z elementów prefabrykowanych z tego materiału można także wznosić budynki wielorodzinne. W takich realizacjach wykorzystuje się prefabrykowane ściany z keramzytobetonu, zazwyczaj trójwarstwowe typu sandwich, z warstwą izolacji i zewnętrznym wykończeniem, np. z betonu architektonicznego. Ściany takie mają bardzo dobrą izolacyjność termiczną i akustyczną. Ze względu na możliwości transportowe wymiary prefabrykatów ściennych nie mogą przekroczyć 9 m długości i 3,65 m wysokości, a ciężar – 8 ton. Prefabrykaty ścienne łączy się zakotwionymi w nich strzemionami lub pętlami stalowymi, przez które przeprowadza się pręt stalowy (zapobiega rozsunięciu się ścian). W miejscu takiego połączenia powstaje kanał, który wypełnia się mieszanką betonową. Ściany są suche, więc nie trzeba ich sezonować tak jak tradycyjnych murów. Uzupełnienie stanowią również keramzytobetonowe stropy.
Producenci prefabrykują niezbędne elementy konstrukcyjne zbrojone prętami, np. nadproża, podciągi lub słupy, wykonują ponadto gotowe schody z betonu.Przykładem obiektu mieszkalnego wykonanego z użyciem prefabrykowanych ścian i stropów keramzytobetonowych jest budynek wielorodzinny przy ul. Bardowskiej w Częstochowie. Prefabrykaty przygotowano wcześniej w fabryce firmy Buszrem, która je dostarczyła i zmontowała z nich kompletną bryłę budynku. Użyte w realizacji elementy keramzytobetonowe wpływają na komfort użytkowania dzięki bardzo dobrej izolacyjności akustycznej, którą potwierdziły badania przeprowadzone w pomieszczeniach częstochowskiego budynku (w stanie deweloperskim).
Elewacja w kolorach białym, pomarańczowym, żółtym i szarym harmonizuje z balustradami balkonów i loggii o konstrukcji stalowej. W czterokondygnacyjnym budynku w kształcie litery L znajduje się 56 funkcjonalnych mieszkań o metrażach od 31 do 58 m². Budynek jest w całości podpiwniczony, głównie dla potrzeb wielostanowiskowego garażu podziemnego. Na dachu została umieszczona kotłownia gazowa zapewniająca ciepło i ciepłą wodę.
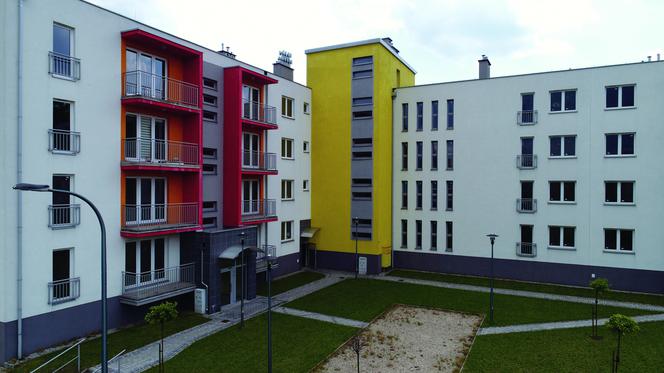
i
Prefabrykaty drewniane
W przypadku konstrukcji drewnianych wyróżnia się prefabrykację otwartą, zaawansowaną i pełną. Pierwsza polega na montażu konstrukcji ściany z poszyciem z płyty drewnopochodnej, uodpornionej na działanie wilgoci (lub włóknowo-gipsowej). Na placu budowy wykonuje się pozostałe prace, m.in. montaż instalacji, izolacji cieplnej oraz stropów i dachu. W prefabrykacji zaawansowanej przygotowane ściany wyposaża się w niezbędne instalacje, izolację cieplną, folię opóźniacza pary i wewnętrzną płytę wykończeniową (np. płyty gk). Pełna dotyczy natomiast wszystkich elementów budynku: ścian zewnętrznych i wewnętrznych, stropów i dachu. Ze względu na wysoki stopień zaawansowania prefabrykacji zakłady wytwarzające elementy budynków o prefabrykowanej konstrukcji drewnianej muszą być wyposażone w wysoko zaawansowane maszyny.
Ściany zewnętrzne domów prefabrykowanych mają ponad 30-centymetrową izolację termiczną, która składa się z wełny mineralnej wypełniającej przestrzenie szkieletu drewnianego oraz płyt styropianowych (najlepiej wielkoformatowych). Dzięki temu o połowę ogranicza się liczbę połączeń, które mogą prowadzić do powstawania mostków termicznych. W przypadku prefabrykowanych domów drewnianych o wyższym standardzie energooszczędności do montażu okien i drzwi zamiast powszechnie stosowanej pianki poliuretanowej wykorzystuje się taśmy rozprężne. Elementy te skutecznie izolują i zapewniają lepszą odporność przeciwwilgociową niż pianka montażowa.
Obecnie coraz częściej zamiast tradycyjnych prefabrykatów o drewnianej konstrukcji szkieletowej stosuje się np. elementy wytwarzane w technologii CLT (z ang. Cross Laminated Timber) lub KLH (z niem. Kross Laminat Holz). Zbudowane są one z desek z litego drewna, w których warstwy skleja się na krzyż za pomocą żywic syntetycznych. Otwory okienne i drzwiowe wykonuje się w fabryce przy użyciu precyzyjnej technologii frezowania sterowanego komputerowo. Maksymalny rozmiar prefabrykatów CLT wynosi 3 x 16 m i są one dostępne w wielu różnych grubościach. Można z nich wznosić budynki do 12 kondygnacji. Elementy mogą być dostarczane w różnym stopniu zaawansowania, w tym z izolacją termiczną, materiałami wykończeniowymi, a także oknami i drzwiami.
Łączenie drewnianych prefabrykatów musi być zaprojektowane tak, by chronić konstrukcję nośną przed przesunięciem lub poderwaniem. Zazwyczaj w ścianach pozostawia się otwory rewizyjne, przez które jest ona kotwiona do podłoża. Wymaga to jednak pracochłonnego wykończenia tych miejsc, dlatego korzystniejszym rozwiązaniem są specjalne złącza kotwiące. Składają się one z dwóch części – górnej, montowanej do drewnianego szkieletu w zakładzie prefabrykacji, i dolnej, mocowanej do fundamentu na budowie. Po złożeniu łączy się je przy użyciu samowiercących wkrętów do stali.Wśród przykładów drewnianych obiektów prefabrykowanych można wymienić ciekawą realizację budynku wielorodzinnego z prefabrykatów drewnianych – apartamentowiec Villa Nova w warszawskiej dzielnicy Włochy, do którego elementy wyprodukowała, dostarczyła i zmontowała firma MultiComfort. To obiekt w standardzie pasywnym, o prostej bryle, z elewacją z naturalnego świerku, który mieści sześć ponadstumetrowych mieszkań. Pod nimi znajduje się garaż podziemny wyłączony z części pasywnej, podobnie jak klatka schodowa wraz z szybem windy.
Ze względów logistycznych wyprodukowano stropy i ściany budynku bez okien i elewacji, ponieważ wymagałyby one bardziej skomplikowanego transportu. Proces prefabrykacji trwał tylko 3 tygodnie – na plac budowy dostarczono szkielet domu wypełniony wełną mineralną (o gr. 150 mm) i obity płytami konstrukcyjnymi Fermacell. Dopiero wtedy zamontowano okna, a także izolację z pianki rezolowej i elewację drewnianą. Do ocieplenia stropodachu wykorzystano wełnę mineralną (o gr. 20 cm) oraz piankę PIR (o gr. 25 cm), nad nimi zaś wykonane są warstwy tarasu odwróconego. Każde z mieszkań ma odrębne zasilanie z powietrznej pompy ciepła – jednostki zewnętrzne zamontowano na dachu, a moduły hydrauliczne w lokalach. Instalację z pompami ciepła połączono z ogrzewaniem podłogowym. W mieszkaniach są również centrale wentylacyjne z odzyskiem ciepła wraz z systemem jego dystrybucji.
Prefabrykaty i budownictwo modułowe
Prefabrykacja w technologii budownictwa modułowego odbywa się w zakładach produkcyjnych równolegle z pracami fundamentowymi, dzięki czemu trwa znacznie krócej niż budowa metodą tradycyjną. Wielkość, wysokość, parametry techniczne i wykończenie można zmodyfikować tak, by budynek spełnił wyznaczone funkcje. Wymiary pojedynczych modułów są każdorazowo optymalizowane pod kątem realizowanego projektu i dostosowane do miejscowych warunków inwestycji. Podstawowe ograniczenie dla wielkości modułów stanowi transport (prowadzony zwykle nocą). Najczęściej ich długość sięga 14–18 m, szerokość 5,5, a wysokość 4,2 m. Produkcja większych jest możliwa, ale musi być poprzedzona szczegółową analizą ekonomiczną i projektową. Konstrukcja modułowa pozwala również na efektywną rozbudowę oraz nadbudowę poprzez dokładanie kolejnych segmentów.
Prefabrykaty o konstrukcji stalowej
Ciekawym przykładem takiego budownictwa są moduły produkowane przez firmę Climatic. Ich konstrukcja nośna ma formę szkieletu ze spawanych, zabezpieczonych antykorozyjnie i ogniochronnie profili stalowych (zimnogiętych lub gorącowalcowanych) o przekrojach wynikających z przeprowadzanych każdorazowo obliczeń statycznych. Konstrukcje spełniają również wymagania w zakresie ochrony przeciwpożarowej. Na ścianach zewnętrznych można zamontować każdy rodzaj systemu elewacji dostępny na rynku. Montaż elewacji wentylowanej oraz stolarki okiennej i drzwiowej w oparciu o bezmostkowy kompozyt konstrukcyjny producenta modułów eliminuje powstawanie mostków cieplnych. Ścianki działowe wykonuje się w oparciu o system suchej zabudowy, co pozwala na łatwą zmianę aranżacji w trakcie użytkowania budynku. Standardowy budynek modułowy wyposażony jest w izolowany termicznie dach płaski z attyką, którego konstrukcja na etapie projektu może być wzmocniona, by można było np. wykonać dach zielony lub zamontować potrzebne urządzenia.
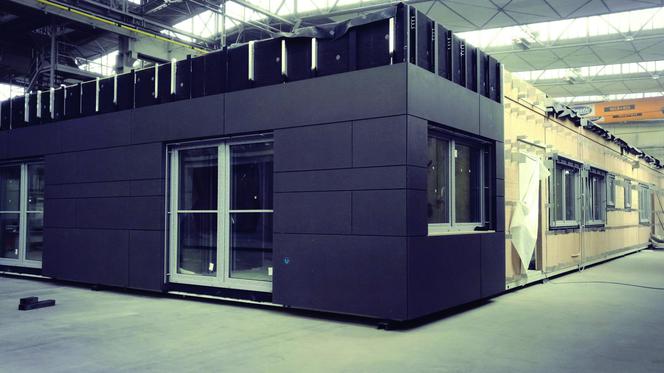
i
Prefabrykaty o konstrukcji drewnianej
Moduły montuje się według dokładnego projektu w fabryce z wyprodukowanych oddzielnie podłóg, ścian i stropów, a następnie wykańcza i wyposaża w niezbędne instalacje: elektryczne, wentylacje, grzewcze, w meble łazienkowe i kuchenne, a nawet sprzęt AGD. Takie rozwiązanie proponuje m.in. firma Unihouse. Element nośny wytwarzanych modułów stanowi szkielet drewniany wypełniony wełną mineralną. Od wewnątrz wykończony jest on płytą gipsowo-kartonową (malowaną, tapetowaną lub obłożoną glazurą), a od strony elewacji dodatkowo ocieplony i otynkowany lub obłożony szalówką bądź cegłą klinkierową. Taki moduł jest sprawdzany pod względem hałasu i szczelności. Moduł może mieć do 14 m długości i do 4,2 m szerokości, i stanowić samodzielne małe mieszkanie – na większe składa się 1,5 modułu lub 2 połączone ze sobą. Kolejne elementy ustawiane są przy użyciu dźwigu. W ten sposób w ciągu 4–5 nocy można wybudować budynek wielorodzinny z kilkudziesięcioma mieszkaniami. Od momentu wyprodukowania modułów do czasu oddania budynku do użytku, np. wielorodzinnego na 30 mieszkań, mija ok. pół roku.
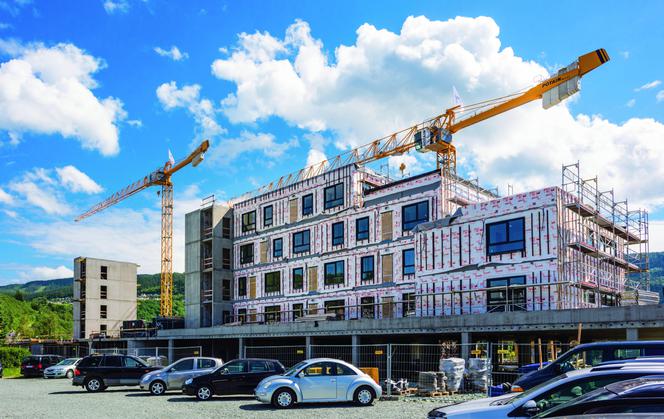
i